MotorSolve can calculate the precise results of the hybrid electric locomotive design, and maintain the simplicity of the templated design environment and result-driven solution. Brushless DC motors, especially the type with embedded permanent magnets, are commonly used in hybrid electric locomotive applications.
Category: Motors and Generators-DC Software: MotorSolve
This type of motor is composed of a salient pole rotor and a reluctance torque element, so the power density is high, the output torque is large, and the speed variation range is wide. The field weakening and constant power variable speed operation is very critical, and no additional transmission device is needed under the condition of wide motor speed range.
The field weakening is achieved by increasing the lead angle, because after the speed is increased, the back EMF is reduced, so it will not exceed the voltage source.
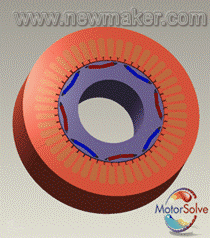
MotorSolve can provide useful analysis results for studying these complex features. MotorSolve's finite element kernel calculation can consider nonlinear materials, PWM pulse width modulation drive circuits, and can establish complex geometric structures through simple wizards.
result
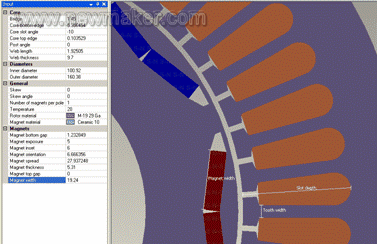
An 8-pole, 48-slot, three-phase embedded magnetic steel motor, although complex in shape, can be built in just a few minutes using MotorSolve's geometric model editor. The stator pole is made of strong permanent magnet material NdFeB, and the rotor salient pole design makes the reluctance torque element operate in a wide speed range.
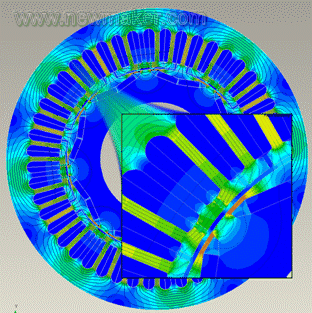
The embedded magnetic steel motor works in the saturation region of the rotor iron yoke, so the characteristics of nonlinear materials need to be considered. The flux diagram at 100A indicates the saturation of the rotor bridge, allowing the designer to optimize the geometric parameters.
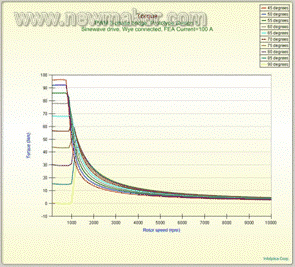
Plotting the torque-speed curve of a motor like the above picture is not an easy task, it needs to be optimized at each speed to obtain the lead angle. MotorSolve can quickly set a variety of combinations of speed and lead angle to draw the above graph. Through the envelope of these curves, the torque-speed curve and the optimized lead angle can be obtained. The curve of the constant power variable speed embedded magnetic steel permanent magnet motor is shown in the figure above.
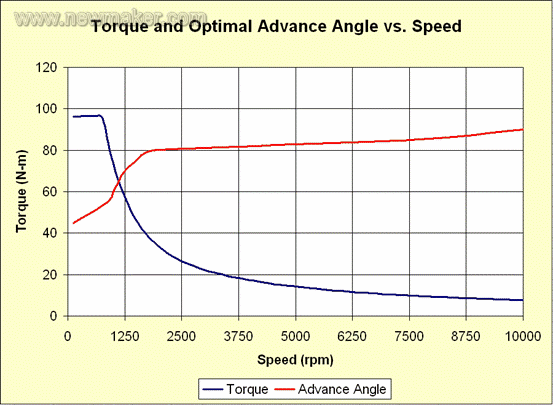
This graph can extract the peak torque at each speed to optimize the lead angle. When the motor exceeds the constant torque area (approximately 875 rpm), the advantage of field weakening becomes prominent.
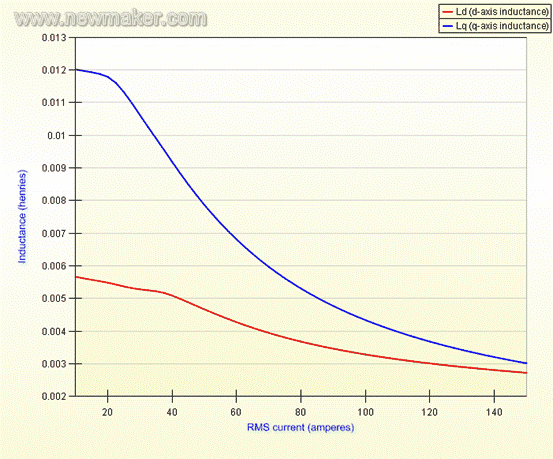
The wide speed range of the embedded magnetic steel permanent magnet motor is due to its high salient pole ratio (d-axis inductance to q-axis inductance ratio). MotorSolve can accurately describe the nonlinear law of inductance caused by magnetic circuit saturation. The figure above shows that Ld and Lq are functions of current.
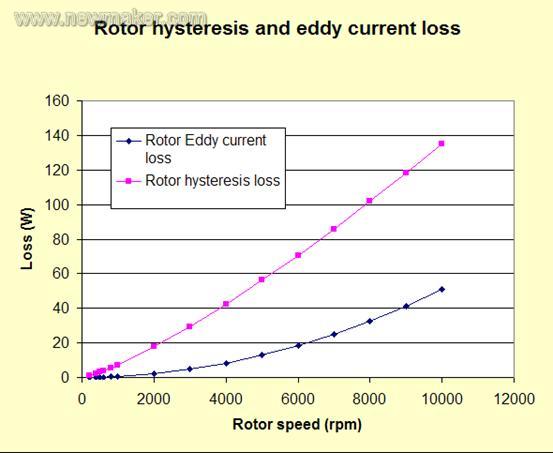
Copper loss is a critical part of the overall loss of the motor. MotorSolve's advanced loss calculation capabilities can calculate component-level hysteresis and eddy current losses. The figure above shows that the rotor's hysteresis and eddy current losses are a function of speed (or equivalently a function of frequency). The eddy current trend is parabolic, and the hysteresis loss is similar to the power curve.
Programmable Controllers Our control solutions set the standard - from the original programmable logic controller (PLC) invented in the 1970s to the technology embodied in the scalable, multi-disciplined and information-enabled programmable automation controller (PAC). Our safety-certified controllers support your SIL 2 and SIL 3 application needs. We offer multiple controller types and sizes to fit your specific needs.
AB Control System Modules
AB Control System Modules,Analog Input Module,Plc Rockwell Controller,Automatic Control System
Xiamen The Anaswers Trade Co,.LTD , https://www.answersplc.com